How Is IoT Making Manufacturing Processes More Efficient?
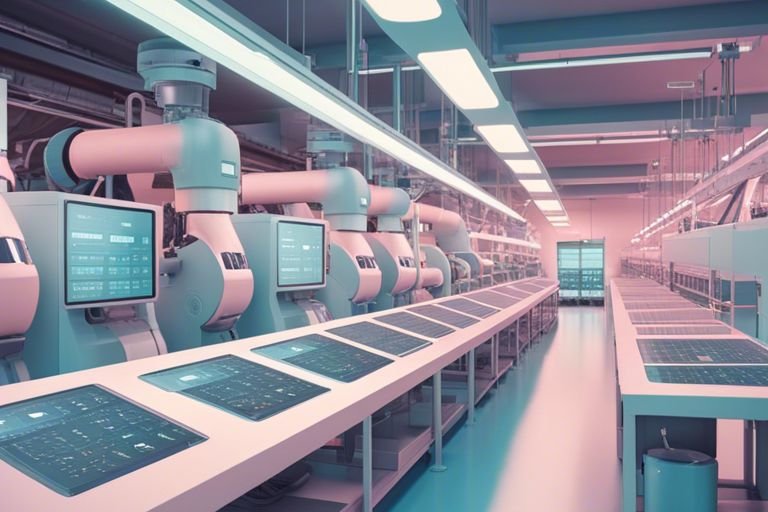
Evaluating the impact of the Internet of Things (IoT) on manufacturing processes reveals a significant increase in efficiency and productivity. IoT has revolutionized the manufacturing industry by providing real-time data for monitoring equipment performance, predictive maintenance, and inventory management. This technology enables manufacturers to optimize their production processes, reduce downtime, and enhance overall operational effectiveness. The integration of IoT in manufacturing has streamlined operations, minimized waste, and improved quality control, ultimately leading to cost savings and a competitive edge in the market.
Key Components of IoT in Manufacturing
To fully understand how IoT is making manufacturing processes more efficient, it’s essential to recognize the key components that make up this technology. These components include sensors and data collection, connectivity solutions, and advanced analytics and reporting tools. Each component plays a crucial role in transforming traditional manufacturing processes into smart, interconnected systems.
Sensors and Data Collection
Collection of real-time data is at the heart of IoT in manufacturing. Sensors are used to monitor various aspects of production, such as machine performance, environmental conditions, and product quality. These sensors continuously gather data, which is then transmitted to a central database for analysis. By collecting and analyzing this data, manufacturers can identify inefficiencies, predict maintenance needs, and optimize production processes.
Connectivity Solutions
One of the fundamental elements of IoT in manufacturing is the connectivity solutions that enable seamless communication between devices and systems. On the factory floor, wireless technologies such as Wi-Fi, Bluetooth, and RFID allow machines and equipment to communicate with each other in real time. Additionally, industrial IoT platforms provide the infrastructure for connecting and managing a vast network of devices, ensuring that data is transmitted securely and reliably. Any disruption or downtime in connectivity can disrupt the entire production process, making robust connectivity solutions crucial for maximizing efficiency and productivity.
IoT-Driven Efficiency Improvements
Now, let’s delve into how IoT is driving significant efficiency improvements in manufacturing processes. By leveraging IoT technologies, manufacturers are able to optimize operations, reduce downtime, and enhance overall productivity.
Predictive Maintenance
For manufacturing plants, unplanned downtime can be costly and disruptive. However, with the implementation of IoT-enabled predictive maintenance, machines and equipment can be continuously monitored for signs of potential failure. This proactive approach allows for timely maintenance and repairs, minimizing the risk of unexpected breakdowns and optimizing equipment uptime.
Real-Time Monitoring and Control
An essential aspect of IoT in manufacturing is the real-time monitoring and control of production processes. This technology provides instant insights into equipment performance, production metrics, and quality control parameters, allowing for immediate adjustments and optimizations. Any deviations or anomalies can be quickly identified and addressed, ensuring consistent product quality and operational efficiency.
Additionally, real-time monitoring enables remote access to critical data, empowering managers and engineers to make informed decisions from anywhere at any time, increasing responsiveness and agility in production management.
Resource and Energy Management
For manufacturers, resource and energy management are crucial factors in maintaining operational efficiency and sustainability. With IoT solutions, facilities can monitor energy consumption, optimize usage patterns, and identify opportunities for efficiency gains. This enables the implementation of energy-saving initiatives, reducing costs and environmental impact while ensuring consistent production output.
This comprehensive approach to resource and energy management aligns with sustainability goals and helps manufacturers to remain competitive in an increasingly environmentally conscious market, all while driving greater operational efficiency and cost savings.
Quality Assurance and Control
An integral aspect of manufacturing is maintaining high-quality standards throughout the production process. IoT technology facilitates advanced quality assurance and control measures, enabling real-time inspection and analysis of product attributes. This proactive approach allows for the early identification of potential quality issues, preventing defects and minimizing waste.
Predictive analytics and machine learning algorithms further enhance quality control by identifying patterns and trends that may impact product quality, allowing for preemptive actions to be taken to ensure consistent and superior product standards.
Case Studies: IoT Success Stories in Manufacturing
For manufacturers, implementing IoT technology has proven to be a game-changer. Let’s take a closer look at some real-life examples of IoT success in manufacturing:
- XYZ Automotive: Reduced maintenance costs by 15% and increased production efficiency by 20% through IoT-enabled predictive maintenance solutions.
- ABC Consumer Goods: Improved supply chain visibility by 30% and reduced inventory holding costs by 25% with IoT-enabled tracking and monitoring systems.
- 123 Heavy Machinery: Decreased downtime by 40% and optimized resource utilization by 25% with IoT-driven real-time monitoring and data analytics.
Automotive Industry Transformations
Success in the automotive industry using IoT technologies has been remarkable. The integration of IoT sensors and data analytics has enabled manufacturers to streamline production processes, monitor equipment performance in real-time, and proactively address maintenance issues.
Advancements in Consumer Goods Production
Automotive IoT has brought about significant advancements in improving consumer goods production. By leveraging IoT devices, manufacturers are able to track and monitor the entire production process in real-time, leading to increased efficiency, reduced waste, and improved overall product quality.
The implementation of IoT devices has brought about a paradigm shift in consumer goods production, revolutionizing the way manufacturers manage their operations and ensure product quality and delivery.
IoT Implementation in Heavy Machinery
Stories of success in heavy machinery are abundant, with IoT implementation leading to significant improvements in operational efficiency, cost reduction, and enhanced equipment performance. Real-time data monitoring and predictive maintenance have been instrumental in transforming the way heavy machinery is managed and maintained.
To capitalize on the benefits of IoT in heavy machinery, manufacturers are embracing cutting-edge technologies to drive innovation, improve operational processes, and achieve sustainable growth in the industry.
Challenges and Considerations
Despite the numerous benefits that IoT brings to manufacturing processes, there are several challenges and considerations that need to be addressed in order to fully leverage its potential.
Security and Privacy Concerns
Any implementation of IoT in manufacturing must take into account the potential security and privacy vulnerabilities that come with the interconnected nature of these systems. With sensitive data and critical operations at stake, the risk of cyber attacks and data breaches is a major concern. Manufacturers need to prioritize robust security measures and privacy protection protocols to safeguard their IoT infrastructure.
Integration with Existing Systems
For manufacturing companies, integrating IoT technologies with existing systems can be a complex and daunting task. It requires careful planning and execution to ensure a seamless integration that does not disrupt ongoing operations. It is essential to consider compatibility, scalability, and interoperability of IoT devices with the existing infrastructure to avoid operational hiccups.
It also involves the adoption of new protocols and standards to ensure that the IoT devices can effectively communicate and collaborate with the existing systems, such as enterprise resource planning (ERP) and manufacturing execution systems (MES).
Skilling and Workforce Adaptation
Privacy The introduction of IoT in manufacturing necessitates a shift in the skill sets and knowledge base of the workforce. As IoT devices become integral to the production process, workers need to adapt and acquire new skills to operate and troubleshoot these technologies. Employers must invest in training and upskilling programs to ensure that their workforce can effectively leverage IoT solutions to enhance manufacturing efficiency.
To address the skilling and workforce adaptation challenges, it is crucial for manufacturing companies to provide comprehensive training on IoT devices, data analytics, and cybersecurity practices. Additionally, fostering a culture of continuous learning and innovation within the workforce is essential to drive the successful adoption of IoT in manufacturing.
Conclusion
Upon reflecting on the impact of IoT on manufacturing processes, it is clear that this technology has significantly improved efficiency in various ways. IoT has allowed for real-time monitoring of equipment, predictive maintenance, and data analytics, resulting in reduced downtime and increased productivity. Additionally, the ability to remotely control and automate processes has streamlined operations and minimized the potential for human error. Overall, IoT has revolutionized the manufacturing industry by providing valuable insights and enabling better decision-making, ultimately leading to more efficient and cost-effective production processes.